/457925963-1600x400.jpg?width=300&name=457925963-1600x400.jpg)
MANAGING CONTRACTOR SAFETY WITH PRE-QUALIFICATION
When contractors and consultants come to your worksite, there are many WHS requirements to follow. First of all, it’s important to select contractors who are properly accredited. You must also ensure that they have a safe working environment and that their equipment is properly maintained to prevent incidents. Conversely, it must be ensured that the activities of the contractors themselves don’t cause harm to others, the environment, the plant or equipment. We recommend everyone in the organisation participates in General Awareness Training for Managing Contractors.
A contractor by definition is a person providing a service to any part of the organisation but who is not an employee. This includes labour hire and subcontractors.
Make sure you have a system in place for the selection of contractors, and a way to monitor their level of accreditation, such as a contractor pre-qualification register. This selection process should take into account:
- licences or registration specific to the work you want the contractor to carry out;
- the contractors' own Health and Safety Management System;
- their personal history of safety and health performance.
A robust Contractor Pre-qualification system ensures your contractors provide documentation that demonstrates the existence and effectiveness of their own Health and Safety Management System. This should include items such as:
- Accident and incident statistics
- A demonstrated system for risk identification and management
- A documented system for specific tasks and work environments – for example, procedures and work instructions
- Records of Health and Safety training
- Records of Health and Safety audits and inspections (particularly for larger contractors)
- Records of prosecutions, and improvement and prohibition notices (if any)
It’s also the manager’s responsibility to regularly monitor the contractor’s activities and ensure compliance with the relevant WHS requirements. How much monitoring is needed depends on the nature of the work the contractor is carrying out. As a guide, high risk activities need almost constant monitoring, whereas low risk activities could perhaps be monitored three times a day – once at the start, once after lunch and then again at the close of the day. It should be noted, however, that this is a general guide only and monitoring levels need to be determined on a case-by-case basis.
Also note that all accidents and incidents involving contractors' personnel must be investigated and reported, and corrective and preventative actions should be applied as soon as practicable. High risk issues should be addressed immediately.
Where a contractor breaches Health and Safety requirements, the appropriate disciplinary measures should be executed right away.
Not necessarily. It is the case that all contractors’ personnel must undergo a comprehensive programme of induction training (including emergency response training). This induction should include entry and registration requirements (for example, site access and the need for identification tags to be displayed or produced upon request).
However, the induction of contractors’ personnel should also be appropriate to:
- The length and nature of the contract
- The hazards associated with the work to be conducted
- The working environment the contractor’s personnel are exposed to
- The level of risk involved in the work
Some organisations have successfully implemented programmes where the induction process and its requirements are directly proportionate to the risk profile of the workers. For example, consultants, sales people, auditors and so on are deemed low-risk and trades such as electricians, builders and labourers deemed high risk, with their induction designed accordingly. This has the effect of matching the use of management resources with the level of worker risk.
Contractor Prequalification
Knowing that your people and your contractors are all qualified and certified in relation to work health and safety before they start work brings peace of mind, and enables you to meet your legislative duty of care. Work Safety Hubs has developed a comprehensive Contractor Prequalification System, utilising online software that:
- assesses health and safety capabilities of contractors and service providers
- ensures appropriate insurances, licenses and trade qualifiactions are in place
- selects contractors based on performance
Contractor safety isn’t set-and-forget; it requires a system built for control and clarity.
Let us help you develop a WHS Management System that ensures contractors and consultants work to your standards, not around them.Download Your Free Checklist PDF
Get instant access to our expert-designed checklist to help you. Simply fill out the form below to download your copy.SIMILAR READINGS
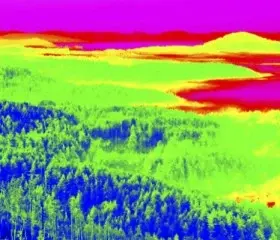
3 min read
3 min read
Australia's great outdoors presents many environmental...
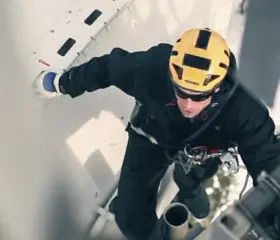
3 min read
3 min read
Falls from heights account for many injuries and fatalities...
Read More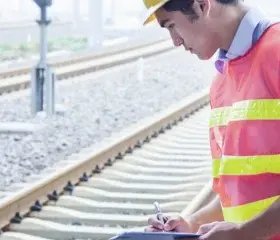
4 min read
4 min read
Seven reasons why strategically managing your health and...
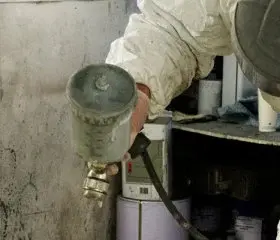
1 min read
1 min read
Are your workers carrying out spray painting tasks in the...
Read More