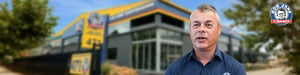
BOB JANE T-MARTS
Elevating Safety with Work Safety Hub: A Journey of Transformation at Bob Jane T-Marts
PROJECT
Reduce Injury Frequency Rate through Improved Safety Systems & Leadership
WHAT WE DID
Initial Review, System Development, Implementation and Support
CLIENT
Bob Jane T-Marts www.bobjane.com.au
TIMELINE
3 Weeks Initial Review, System Development 8 weeks, Support Implementation 12 months
JOURNEY TO IMPROVEMENT
As Australia's premier independent retailer and franchise in the tyre service industry, Bob Jane T-Marts has set benchmarks with over 130 locations nationwide. However, the challenge of escalating workplace injuries, including severe musculoskeletal incidents, called for an innovative approach to safety management. Leaders at Bob Jane, including National Risk Manager Angelo Bootlis, National Operations Manager Sam Mari, and CEO Rodney Jane, sought Work Safety Hub's expertise to spearhead a shift towards exemplary safety performance, embodying our 'Safety Differently' philosophy.
Initial assessments illuminated a reactive, compliance-driven safety culture at Bob Jane. Despite some strengths, the overarching safety goals and management knowledge fell short of propelling Bob Jane to the forefront of industry safety standards. Recognising these gaps, Work Safety Hub and Bob Jane charted a course for significant cultural transformation and operational enhancement.
The partnership aimed at reducing injuries and revolutionising Bob Jane's safety culture from reactive to resilient, as outlined in the Hudson and Parker Culture Ladder. This ambitious plan involved elevating line organisation skills for comprehensive safety management across all operations.
CHALLENGES
- Safety professionals felt trapped in a compliance focused activity cycle rather than meaningful safety improvements
- The focus was often on paperwork and procedures rather than real safety outcomes
- Safety professionals struggled to get senior management to truly engage
- Safety work was often reactive rather than proactive
- Safety Management System design & development from scratch is not feasible
- Client would like to be able to hit the ground running
- Safety Management System must be implemented in multiple states and languages
- Safety Management System must conform with numerous Australian Standards
Moving safety forward
RESULTS
- Safety as an Enabler – Not an Administrative Burden
Bob Jane T-Marts transitioned from viewing safety as a cost centre to recognising it as a driver of operational reliability and business success. - Leadership Engagement: Executive and operational leaders began to see safety not as ‘red tape,’ but as an investment in operational excellence and workforce wellbeing.
- Decisions Shaped by Work Realities: Safety conversations shifted from theoretical policies to practical, operationally aligned discussions—resulting in decisions that better supported frontline work.
- Increased Leadership Visibility: Senior leaders became more actively engaged in observing work and understanding the realities faced by their teams.
- From Compliance to Capability
Previously, safety work focused heavily on documentation and task completion. We refocused the approach towards building the capacity to handle work variability and unexpected challenges. - Simplified, User-Centric System: The Safety Management System was designed to be intuitive and fit-for-purpose, ensuring frontline teams could easily engage with it.
- Focus on Safe Adaptation: Teams were empowered to manage risk dynamically, making informed adjustments based on local knowledge and changing conditions—rather than rigid rule-following.
- Reduced ‘Tick-the-Box’ Culture: Safety became less about checklists and more about conversations—focusing on how work is done safely, even when things don’t go to plan.
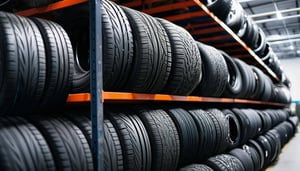
"Partnering with Work Safety Hub has transformed the way we approach safety at Bob Jane T-Marts. We’ve seen a real shift – from viewing safety as a compliance obligation to recognising it as a driver of operational resilience and business success. Leadership is more engaged, our teams feel empowered to speak up and adapt when needed, and we’ve reduced operational disruptions related to safety incidents. Safety is no longer just about paperwork; it’s about enabling better work, every day. That’s what moving safety forward really looks like."
Angelo BootlisNational Risk Manager