/147288297-1600x400.jpg?width=300&name=147288297-1600x400.jpg)
The Most Effective Approaches to WHS Risk Management
Proactive Risk Identification: The Foundation of Safer Work
Actively anticipating and identifying potential risks and hazards in the workplace is one of the most effective ways to prevent harm and support successful work. While all businesses must meet WHS obligations, focusing on risk reduction is not just a compliance exercise—it’s an investment in operational stability, wellbeing, and sustainable performance.
Creating a safe working environment involves developing safeguards, controls, and work processes that reduce exposure to harm—not just for workers, but for everyone impacted by the organisation’s operations. Hazards can lead to outcomes ranging from minor disruptions to severe injury or fatality. This guide outlines key strategies and practices for understanding, managing, and reducing workplace risk.
Communication and consultation
Risk management is most effective when it’s done with people, not to them. This means moving from telling to asking—engaging workers, leaders, contractors, and others in conversations about risk, controls, and work realities. A well-developed communication and consultation plan ensures that safety decisions reflect diverse perspectives and operational knowledge.
The plan should:
- Identify those affected by the risk and involve them early.
- Clarify who is responsible for implementing controls.
- Explain the basis for decisions and why actions are required.
- Provide mechanisms for ongoing engagement and learning.
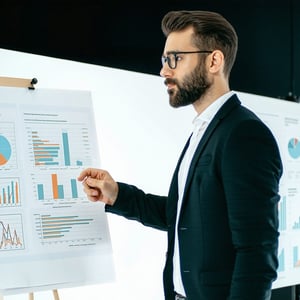
The scope and sensitivity of the plan should be proportionate to the risk and must identify:
Hazards are often hidden in plain sight—embedded in how work is structured, resourced, and performed. Effective hazard identification methods include:
-
Observations and walkthroughs, including peer-based and specialist inspections.
-
Review of safety-critical processes (e.g., confined space, plant movement, chemical handling).
-
Insights from incident data, near misses, and learning reviews.
-
Worker-raised concerns and frontline experience, which often highlight what systems overlook.
All identified hazards should be recorded, and where applicable, trigger a Corrective Action or Learning Review process—not just to fix, but to understand.
Risk assessments should focus on how work is done, not just how it was imagined or documented. The purpose is to evaluate:
-
Likelihood of the hazard leading to harm.
-
Consequences of that harm.
-
Exposure to the hazard.
When deciding what is "reasonably practicable", consider:
-
Known and foreseeable factors.
-
Control availability and suitability.
-
The cost, effort, and potential trade-offs of additional controls.
Risk assessments should be refreshed when:
-
New equipment or processes are introduced.
-
There are changes to tasks, people, or conditions.
-
Evidence suggests current controls are no longer effective.
For high-risk scenarios, or where trade-offs between risks must be made (e.g., low-frequency high-consequence vs high-frequency low-consequence), a Quantitative Risk Assessment (QRA) and specialist input may be warranted.
Considering the Design of Work and Plant
When assessing plant and equipment, examine:
- Suitability of design and placement.
- Impact of wear, corrosion, modification, or poor maintenance.
- Human interaction: access, visibility, use of controls.
- Historical data on breakdowns, near misses, or misuse.
Don’t forget that how work is done often deviates from procedures. Involve those who operate, maintain, and interact with the plant to surface actual conditions and challenges.
Using the Hierarchy of Controls
Controls are not equal. The Hierarchy of Controls provides a structured way to prioritise risk reduction:
- Eliminate the hazard altogether.
- Substitute with something less hazardous.
- Isolate people from the hazard.
- Engineer out the risk.
- Use Administrative controls (procedures, training, planning).
- Provide Personal Protective Equipment (PPE) as the final layer.
Control decisions should be informed by effectiveness, not just convenience or cost. Engineering and substitution are often underused in favour of administrative controls that rely heavily on worker behaviour.
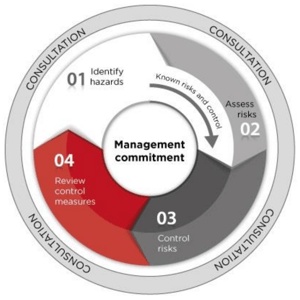
Controls can degrade, drift, or be bypassed. Ensure you:
-
Verify that controls are present, used, and functioning.
-
Identify defeating factors—things that can make a control ineffective.
-
Maintain, test, and inspect safety-critical systems.
-
Track the completion of critical activities as leading indicators of safety performance.
Remember, controls should be designed with the realities of work in mind—not just idealised versions of tasks.
Regular reviews are vital. Reassess when:
-
An incident or near miss indicates a gap in your controls.
-
Work conditions or structures change significantly.
-
Stakeholder feedback or data suggest assumptions no longer hold.
Reviews should not only consider technical performance but also how people experience and adapt to risk controls in practice.
Effective hazard and risk management is not about eliminating every possible hazard—it’s about making wise, informed decisions about which risks matter most and how to reduce them so far as is reasonably practicable (SFAIRP). It’s about supporting people to do work well, even when things don’t go to plan.
As a safety leader, your role is to:
-
Foster curiosity about how work is really done.
-
Engage in humble inquiry, not assumptions.
-
Coach and support others to build capacity, not just compliance.
By shifting from enforcing rules to understanding and improving how work happens, we build organisations that are not only safer—but more resilient, adaptive, and human-centred.
Download Your Free Checklist PDF
Get instant access to our expert-designed checklist to help you. Simply fill out the form below to download your copy.Effective risk management starts with a system that works.
We’ll help you design a WHS Management System that systematically identifies, assesses, and controls hazards—driving safer outcomes every day.SIMILAR READINGS
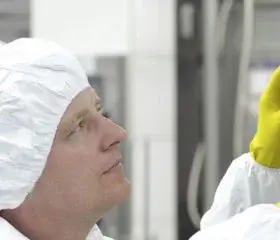
2 min read
2 min read
Conduct your next audit with minimum of fuss and maximum...
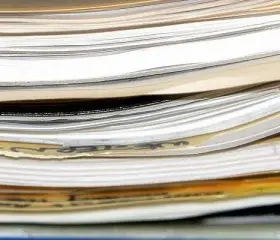
1 min read
1 min read
As a business owner, it’s your responsibility to ensure...
Read More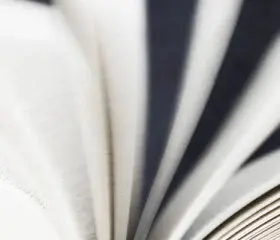
2 min read
2 min read
Many WH&S manuals are missing five important items from their text....
Read More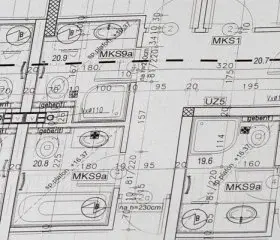
3 min read
3 min read
How the Australian Standards are used in court proceedings...
Read More