/483170835-1600x400-1.jpg?width=300&name=483170835-1600x400-1.jpg)
EFFECTIVE WHS SAFETY AUDIT PROCESSES
The Critical Role of Safety Auditing in Workplace Health and Safety
Safety Auditing plays a pivotal role in ensuring the efficiency and effectiveness of health and safety management systems within any organisation. It involves a comprehensive, formal, and systematic examination of your systems, procedures, and work practices. This documented review is essential to verify that they not only comply with the stringent requirements of your Workplace Health and Safety (WHS) Management System but also ensure their effective implementation across all levels of your organisation. By doing so, safety audits serve as a critical checkpoint to maintain high standards of safety and operational excellence.
Conducting thorough safety audits is instrumental in identifying any existing gaps or weaknesses within your system. These audits provide a clear roadmap for planning corrective actions, enabling you to address and close these gaps efficiently. This proactive approach not only mitigates potential risks but also fosters a culture of continuous improvement, ensuring that your processes evolve and adapt to meet emerging safety challenges and regulatory demands.
To assist you in enhancing the success of your safety assessments, this guide presents a collection of techniques and insights from our team of expert safety auditors. These professionals bring a wealth of experience and knowledge to the audit management process, equipping you with the tools and strategies needed to conduct more effective and insightful assessments. By leveraging their expertise, you can elevate your safety auditing practices, ensuring that your organization remains at the forefront of health and safety management.
Safety Audits should be conducted in accordance with a meticulously planned and agreed-upon controlled audit schedule. This schedule serves as a strategic framework, ensuring that audits are systematically carried out at regular intervals, thereby maintaining a consistent oversight of safety practices. However, there are circumstances where unscheduled audits may become necessary. These can be prompted by unexpected incidents, changes in operations, or emerging risks that require immediate attention. In such cases, it is crucial to notify auditees in advance of any impending audits, whenever feasible, to ensure transparency and cooperation.
Internal Safety Audits should be conducted at least once a year as a baseline standard. This annual review is essential for maintaining a robust safety management system. However, the actual frequency of audits for specific work areas or operational aspects should be more dynamic and responsive to the unique conditions of each environment. This means that the frequency should be tailored based on a thorough assessment of the level of risk associated with each area and the specific nature of hazards identified. High-risk areas may require more frequent audits to ensure that safety measures are effectively mitigating potential dangers, while lower-risk areas might be audited less frequently, allowing resources to be allocated where they are most needed. This risk-based approach ensures that safety audits are not only regular but also relevant and impactful, fostering a proactive culture of safety within the organization.
Conduct of the Safety Audit
Safety Audits should commence with a structured opening meeting and conclude with a closing meeting, both of which are integral to the audit process. These meetings, while not mandatory for internal safety audits due to site expectations, are crucial for external audits. They are attended by the audit team and the auditee(s) to establish a clear understanding of the audit's scope, objectives, and any specific areas of focus. The opening meeting sets the stage for the audit, ensuring that all parties are aligned and aware of the procedures to be followed. The closing meeting, on the other hand, provides an opportunity to discuss preliminary findings, address any immediate concerns, and outline the next steps.
Safety Management System Audits are most effectively conducted through a meticulous examination of relevant documents, practices, and other tangible evidence. This process is complemented by interviews with personnel, which offer valuable insights into the practical application of safety protocols and the overall safety culture within the organisation. It is imperative that personnel being audited fully cooperate with the Safety Auditor, providing any requested information promptly and accurately. This cooperation is essential for a comprehensive and accurate assessment of the safety management system.
A thorough safety audit encompasses several critical components, including but not limited to:
- Compliance with the organisation’s Workplace Health and Safety (WHS) requirements, which include detailed policies, procedures, and work instructions designed to uphold safety standards.
- Adherence to all applicable legislative requirements, ensuring that the organisation meets or exceeds the legal standards set forth by regulatory bodies.
During the audit, any instances of non-compliance are meticulously documented through a Non-compliance Note, also known as a Non-conformance Request. Each identified non-compliance is carefully evaluated and prioritised based on its potential impact on safety and operations. This prioritisation allows the organisation to address the most critical issues first, ensuring that corrective actions are implemented efficiently and effectively to enhance overall safety performance.
Safety Audit Report
A comprehensive report that meticulously summarises the outcome of the safety audit is typically prepared and subsequently issued to both the Auditee(s) and the Site Manager. This detailed document serves as a crucial communication tool, encapsulating the findings, observations, and recommendations derived from the audit process. It provides a clear and structured overview of the audit's scope, the methodologies employed, and the specific areas examined. Furthermore, the report highlights any instances of non-compliance, potential risks, and areas for improvement, offering actionable insights and guidance for enhancing safety practices. By delivering this report, the organisation ensures that all relevant stakeholders are informed and equipped to take necessary corrective actions, thereby reinforcing a culture of safety and continuous improvement within the workplace.
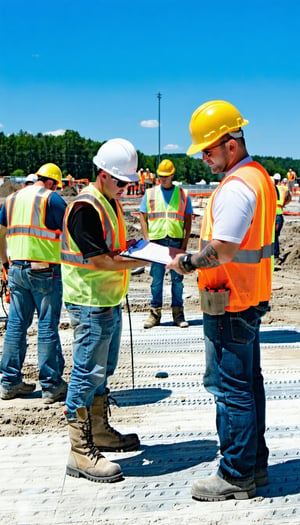
Scope-specific Safety Audits and Assessments
To maintain a robust and compliant safety management system, it is imperative that comprehensive arrangements are established to guarantee that all necessary scope-specific safety audits and assessments are conducted at the designated intervals. These arrangements are not merely procedural but are essential to ensure adherence to legislative requirements and industry standards. They should encompass a wide range of audits and assessments, each tailored to address specific operational needs and regulatory mandates.
For instance, audits related to electrical installations and equipment are crucial to verify that all electrical systems are functioning safely and efficiently, minimising the risk of electrical hazards. Similarly, plant audits are vital to assess the safety and operational integrity of machinery and equipment, ensuring they meet safety standards and do not pose any risk to workers.
Beyond these, it is essential to include any other audits and assessments that are pertinent to the unique operations of the organisation. This could involve evaluating safety protocols in specialised areas, such as chemical handling, fire safety, or ergonomic assessments, depending on the nature of the business. By implementing these comprehensive arrangements, organisations can proactively manage safety risks, ensure compliance with legal obligations, and foster a culture of safety and continuous improvement across all operational facets.
External Authorities
In the event of an audit conducted by a government authority, it is imperative that the responsible manager undertakes a thorough review of the audit's outcome. This review should focus particularly on any mandatory actions and notices issued as a result of the audit. It is crucial to meticulously assess these findings to determine their accuracy and reasonableness. Should any findings, actions, or notices appear to be inaccurate or unreasonable, the manager has the right to challenge them. In such cases, it is essential to compile and present robust supporting evidence to substantiate the challenge, ensuring that the auditor is provided with a comprehensive rationale for the dispute. Conversely, any actions or notices that are deemed accurate and have been accepted should be promptly addressed through a well-structured corrective action plan. This plan should outline specific steps and timelines to ensure that these actions are completed efficiently and effectively, thereby reinforcing the organisation's commitment to compliance and continuous improvement.
Our team of highly qualified and experienced safety auditors significantly enhances the audit process by integrating evidence-based best practices derived from the latest research. Their expertise not only ensures that audits are conducted with the highest level of professionalism and accuracy but also provides your organisation with valuable insights and strategies for ongoing improvement. By staying abreast of the latest developments in safety management, our auditors empower your organisation to continuously refine and elevate its safety practices, ensuring that you remain at the forefront of health and safety excellence.