The construction industry is renowned for its focus on safety compliance, a critical aspect to ensure the wellbeing of workers, prevent incidents, and meet regulatory requirements. However, for smaller contractors in allied trades, such as painters, plumbers, tilers, electricians, carpenters, concreters, roofers, and bricklayers, this demand for compliance can become an overwhelming burden. Larger constructors frequently require these trades to maintain the same level of documentation and safety compliance as bigger companies, even when their resources and teams are much smaller. The result is often excessive bureaucracy, draining time and energy from small businesses and impacting their operational performance.
This article explores the pain points of this issue and highlights how automating safety processes and adopting trade specific safety management software can alleviate the burden, allowing these businesses to focus on what they do best: delivering high quality craftsmanship.
The Compliance Challenge for Allied Trades
For many trade contractors, maintaining safety compliance can feel like an endless uphill battle. Larger constructors require detailed documentation, including Safe Work Method Statements (SWMS), incident reports, risk assessments, and various permits. This often places smaller contractors in a difficult position, as they are expected to uphold these stringent standards while lacking the resources, manpower, and administrative infrastructure of larger companies.
Common pain points include:
- Excessive paperwork: Hours spent filling out forms and producing documents, time that could otherwise be spent on productive work.
- Inefficient manual processes: Tracking compliance manually is error prone, leading to potential delays, missed deadlines, or incomplete reports.
- Complex regulatory requirements: Regulations are constantly changing, and staying up to date without dedicated safety personnel can be challenging for smaller organisations.
- Pressure from larger contractors: Working with large construction firms often brings the added requirement of meeting their complex safety protocols, which are designed for much larger organisations with dedicated safety teams.
For small businesses with limited staff, these pain points result in significant inefficiencies, causing frustration, bottlenecks, and even lost opportunities.
The Benefits of Automating Safety Processes without Sacrificing Safety Outcomes
One of the most effective ways to alleviate these pain points is through the automation of safety compliance processes. Leveraging technology to streamline safety documentation and procedures can drastically reduce the time, effort, and risk of error associated with manual systems. Here's how:
1. Time Savings through Automation
Automating safety processes can significantly reduce the time spent on paperwork. Instead of manually preparing SWMS or incident reports, software can automatically generate these documents based on predefined templates. The data can be reused across projects, meaning tradespeople only need to input information once, dramatically cutting down on repetitive tasks. This time-saving benefit allows smaller contractors to focus more on project delivery, client relationships, and improving their craft.
2. Improved Accuracy and Compliance
Human error is a common challenge in manual compliance tracking. Mistakes in documentation can lead to costly delays, non-compliance penalties, or safety incidents. An automated solution ensures consistency and accuracy in record-keeping, significantly reducing the risk of errors. Furthermore, automated systems can be updated to align with changing regulations, helping smaller trades stay compliant without having to constantly monitor legal updates.
3. Industry Specific Solutions for Greater Relevance
Generic safety management systems often fail to address the unique needs of various trades. A solution specifically tailored to allied construction trades allows each contractor, whether a painter, plumber, or roofer, to use tools and processes relevant to their line of work. For instance, a painter might need quick access to material safety data sheets (MSDS), while a roofer may require specific risk assessment templates for working at heights. Having a customised solution means that each trade can meet safety standards without being overwhelmed by irrelevant features or documentation requirements.
4. Seamless Collaboration with Larger Contractors
Smaller trades often struggle to meet the safety documentation standards imposed by larger construction firms. With an automated safety management solution, these trades can easily share the necessary compliance documents, reports, and safety records, ensuring a smooth collaboration. Pre-populated forms and templates ensure that these documents are professionally formatted and complete, meeting the standards of the larger companies without placing an undue burden on the smaller contractor.
5. Real-Time Tracking and Reporting
Traditional methods of tracking incidents or compliance require sifting through paper records or manually updating spreadsheets. An automated system allows for real-time tracking of incidents, near misses, and safety actions, giving contractors a clear picture of safety performance at any given time. Automated reports can be generated and shared with stakeholders, helping to maintain transparency and compliance throughout the project lifecycle.
6. Reducing Administrative Overhead
One of the greatest burdens for smaller contractors is the administrative load that compliance places on them. Automating the process reduces the need for dedicated staff or external consultants to manage safety paperwork. In turn, this lowers operational costs and allows small businesses to operate more efficiently with leaner teams.
Introducing a Low Cost Trade Specific Safety Management Solution
Recognising the unique challenges faced by allied construction trades, we’ve developed a safety management software tailored to the needs of each trade. Our solution is designed with simplicity and functionality at its core, ensuring that safety processes are streamlined without compromising compliance or performance.
Key features of the software include:
- Customisable templates for SWMS, risk assessments, and incident reporting: Each trade has access to industry-specific templates, reducing the complexity and time spent on documentation.
- Automated document generation and submission: Safety reports and compliance documents are automatically generated and can be shared with larger contractors or regulatory bodies.
- Real-time updates on regulatory changes: Stay informed of changing safety regulations with automatic updates, ensuring ongoing compliance without manual effort.
- Mobile access for on-site safety management: The software is fully mobile-enabled, allowing contractors to access safety information, submit reports, and complete documentation from anywhere on the job site.
A Path Forward for Allied Construction Trades
The burden of safety compliance doesn't have to weigh down small contractors in allied construction trades. By adopting an automated, industry specific safety management solution, painters, plumbers, tilers, electricians, and many others can streamline their processes, reduce administrative overhead, and improve overall efficiency. Automation offers the tools to not only comply with the rigorous demands of larger constructors but to enhance safety performance without sacrificing productivity.
By investing in the right safety management software, allied trades can shift their focus from cumbersome paperwork to doing what they do best, delivering exceptional, high quality work while staying compliant, safe, and competitive in the industry.
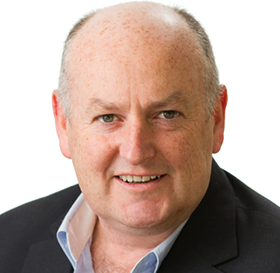