In every organisation, safety is a critical priority, with leaders often setting ambitious safety goals to protect their workforce. Despite these good intentions, many safety programs fail to deliver the expected results. The root cause often lies not in the lack of resources or commitment but in strategic misalignment—where safety goals are disconnected from the daily activities that drive operations.
This article explores the concept of strategic safety misalignment, identifies the reasons it occurs, and offers practical steps to ensure that safety programs are aligned with the realities of day-to-day work and that they succeed.
What is Strategic Safety Misalignment?
Strategic safety misalignment refers to the gap between an organisation’s stated safety goals and the actual behaviors, practices, and operations happening daily on the ground. This gap often arises when safety is viewed as an isolated initiative, separate from the core business functions, or when the pursuit of operational efficiency takes precedence over safety.
Key characteristics of strategic safety misalignment include:
- Top-down safety goals that are not integrated into daily operations: Leadership may set ambitious safety targets, but workers may not see how their actions directly contribute to those goals.
- Conflicting priorities between safety and productivity: If workers are incentivised to prioritise output over safety, this conflict can erode the effectiveness of safety programs.
- Lack of feedback loops between safety initiatives and operational realities: Safety programs often fail to evolve in response to changing workplace conditions, making them less relevant over time.
Why Does Strategic Misalignment Occur?
1. Disconnection Between Safety and Business Goals
Many organisations treat safety as a separate function rather than integrating it with their overall business strategy. While companies may have clear safety goals, they often fail to link these goals with other business priorities like productivity, profitability, or customer satisfaction. This creates a situation where safety becomes a secondary concern when weighed against the pressure to meet production deadlines or cost targets.
2. Lack of Operational Ownership
Safety programs are sometimes seen as the responsibility of the safety department alone, rather than something that every manager and employee is accountable for. When safety is viewed as an external function, it’s easy for daily operational decisions to sideline safety considerations in favor of short-term objectives, such as meeting quotas or deadlines.
3. Insufficient Leadership Involvement
While senior leadership often initiates safety programs, there can be a disconnect between leadership’s vision and the reality faced by workers. Leaders may set safety goals, but without regular involvement or follow-up, those goals may not be prioritised in day-to-day decision-making. Without active leadership engagement, safety becomes a passive activity, and workers may interpret it as less important than operational efficiency.
4. Inconsistent Communication
Safety goals and initiatives must be clearly communicated throughout the organisation, from the executive level down to frontline workers. Often, safety messages don’t trickle down effectively, or workers don’t fully understand the link between their tasks and the organisation’s safety objectives. This results in inconsistency in applying safety protocols, undermining their effectiveness.
5. Misaligned Incentives
In many workplaces, productivity metrics and financial performance are more closely tied to rewards than safety performance. If employees feel that their success is measured more by how quickly they complete tasks than by how safely they perform them, they may take shortcuts that compromise safety. This misalignment of incentives can lead to an erosion of safety practices, even when safety programs are in place.
The Impact of Strategic Misalignment on Safety Programs
When safety programs and daily operations are not aligned, several negative outcomes can emerge:
1. Decreased Safety Performance
Even with safety procedures in place, misalignment can lead to inconsistent application of these procedures, increasing the likelihood of accidents and incidents. Workers may not see the relevance of safety measures, or they may ignore them in favor of faster, more efficient ways to complete their tasks.
2. False Sense of Security
Organisations may believe they are operating safely because they have implemented safety policies or completed safety training. However, without a clear connection to daily operations, these safety initiatives can become mere checklists, giving the illusion of safety rather than genuine risk reduction.
3. Compliance Without Real Safety
Many organisations focus on compliance audits and meeting regulatory requirements, assuming that if they are compliant, they are safe. However, compliance alone does not ensure that safety systems are effective in real-world conditions. Without operational alignment, organisations may pass audits but still face significant risks in their day-to-day activities.
4. Reduced Employee Engagement
When workers feel that safety initiatives are imposed from the top without considering their daily challenges, they are less likely to engage with those initiatives. This lack of buy-in can lead to low morale, resistance to change, and a general disregard for safety protocols.
How to Achieve Strategic Alignment Between Safety Goals and Daily Operations
To prevent strategic misalignment, organisations must create an environment where safety goals are fully integrated into everyday activities. This requires an approach that involves leadership, management, and workers at every level. Here are some key strategies to achieve this alignment:
1. Embed Safety Into Core Business Strategy
Safety should not be a separate initiative; it should be part of the organisation's core strategy. This means integrating safety into every business goal, whether related to productivity, profitability, or customer satisfaction. When safety is aligned with other business priorities, it becomes part of how work is done, rather than something additional that workers have to think about.
2. Leadership Commitment and Role Modeling
Leaders play a crucial role in aligning safety with operations. They must actively demonstrate their commitment to safety by embedding it into their daily decision-making and communications. When leadership models safe behaviors, it signals to the rest of the organisation that safety is a priority. Leaders should also hold regular safety discussions, not only in safety meetings but in all business meetings, reinforcing that safety is integral to success.
3. Operational Ownership of Safety
Safety should be the responsibility of everyone in the organisation, not just the safety department. Managers at all levels should be accountable for ensuring that safety protocols are followed in their departments. This can be achieved by incorporating safety performance into management KPIs, making safety a measure of operational success.
4. Align Incentives With Safety
To avoid conflicting priorities, companies must ensure that their incentive structures reward safe behavior as much as productivity and efficiency. For example, performance appraisals should include safety metrics, such as participation in safety training, adherence to safety protocols, and incident-free workdays. When safety becomes a key metric for success, employees are more likely to prioritise it.
5. Foster a Culture of Safety Communication
Communication is essential for aligning safety goals with daily activities. Safety goals should be communicated clearly and regularly, with a focus on how each employee’s tasks contribute to overall safety objectives. Managers should engage with workers to gather feedback on how safety initiatives are working in practice and adjust plans based on this feedback. This creates a continuous feedback loop that keeps safety relevant and adaptable to changing conditions.
6. Monitor and Adjust Safety Programs
Safety is not a one-time initiative but an ongoing process. Organisations should regularly monitor the effectiveness of their safety programs by tracking leading indicators, such as the completion of safety inspections, worker engagement in safety activities, and near-miss reporting. This data should be used to refine and adjust safety strategies as needed, ensuring that they remain aligned with operational realities.
Conclusion: Aligning Safety and Operations for Long-Term Success
Strategic safety misalignment is a common but avoidable issue in many organisations. When safety goals and daily activities are not aligned, safety programs can fail, leaving organisations vulnerable to accidents, increased risks, and disengaged workers. To avoid this, companies must integrate safety into their core business strategy, ensure leadership commitment, align incentives, and foster a culture of open communication.
By making safety a fundamental part of everyday operations and ensuring that it is as much a priority as productivity or profitability, organisations can create a safer, more engaged, and more efficient workplace. Aligning safety with operations is not just about meeting goals—it’s about embedding safety into the DNA of how work gets done.
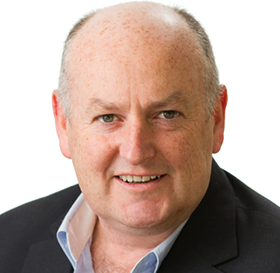