Here we help you understand your obligations in relation to emergency equipment, including emergency washing equipment such as eye-bath and drench showers, warning lights, alarms, siren and evacuation lighting. We discuss purchasing, inspections and maintenance also.
Question1: Where should emergency equipment be located?
A Hazard Identification process should be conducted to identify all locations where emergency equipment may be required.
This should include equipment such as:
- Fire fighting equipment
- Drench showers and eye-baths where workers are at risk of being in contact with harmful substances (particularly corrosive substances such as acids).
- Spill control equipment
- Transport spill control equipment.
Emergency equipment should be located in easily accessible locations and within a reasonable distance from the source of hazard. Such locations should be sign-posted, including directions from areas where they cannot be seen.
Question 2: Is training required?
All personnel should be trained so that they are thoroughly familiar with the locations of all emergency equipment and the correct method for using them. Familiarity with emergency equipment locations and use, should form part of the induction training process.
Question 3:What about emergency devices and lights?
Warning devices such as lights, sirens, bells, etc should be installed in all locations where personnel need to be warned of a hazard or an emergency (e.g. over pressure, release of toxic gasses, etc). Refer Australian Standard AS 2220. Emergency evacuation lighting, in accordance Australian Standard 2293 and Local Government requirements should be installed, and regularly inspected and maintained.
Question 4: Do we need emergency power supply?
Emergency power supply (independent of the normal mains supply) should be provided for all plant and equipment which may present a significant WH&S risk in the event of an interruption to their normal power supply.
This should also apply to equipment required in the event of an emergency (e.g. fire, pumps, extraction fans, etc) and to instrumentation and control systems necessary for safe shut- down.
Where required, battery-powered emergency supply should also be provided (e.g. for control systems).
Emergency power supply systems should be inspected and tested in accordance with a formal schedule.
Question 5: Inspection and Maintenance?
Emergency equipment should be regularly inspected and maintained to ensure it is in proper working order and a state of readiness.
Qualified personnel, in accordance with controlled inspections check sheets, should carry out inspections.
Full records of inspections and testing of emergency equipment should also be kept.
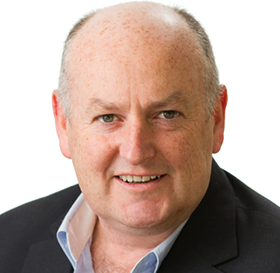