In this article we discuss five practical steps you can follow to ensure your organisation is compliant with its legal obligations, including the requirements of all acts, regulations, standards and other licences relevant to your business. We discuss the establishment of a requirements library, tracking changes to requirements, accessing this information, providing personnel with documented instructions, certificates of competency, dealing with authorities and civil penalties.
The five steps are:
Step 1. Establish a legal requirements library
A controlled library should be established with copies of all Work Health and Safety commonwealth, state, statutory authorities and local government acts, regulations, codes of practice and Australian Standards relevant to your organisation.
A system should be established to maintain the library up-to-date and ensure that amendments (e.g. of acts, regulations, Australian Standards, etc) are incorporated in your procedures and work instructions as soon as they are issued.
Copies of documents in the library must be easily accessible to personnel who may need them. These persons should always be advised of amendments of external documents related to their responsibilities, as soon as practicable.
Step 2. Advise Directors’ and Managers’ of their responsibilities
Chief Executives, General Managers, Managers and Supervisors need to ensure that all personnel are provided with clear, documented procedures and instruction to define how work is to be carried out safely and in compliance with all the relevant legislative requires, since in many jurisdictions 'lack of knowledge' does not constitute a valid defence in the event of a prosecution.
Managers need to be formally advised that in jurisdictions where industrial manslaughter is in force individuals can face imprisonment if found guilty of industrial manslaughter (i.e. a fatality, where criminally reckless or criminally negligent behaviour on the part of the officer has been proven. In all instances where such circumstances may eventuate, legal advice must be urgently sought.
In addition, managers must be formally advised that in some jurisdictions jail sentences can be given to offenders for ‘gross negligence’ – that is, where there was a disregard for the likelihood of death or serious harm occurring and, where death or serious injury did result from the contravention.
Step 3. Ensure government authorities and right of entry procedures are understood
Approved inspectors from authorities must be given right of entry, the requested information and the required cooperation, in accordance with the requirements of the relevant legislation.
Where approved by legislation persons who are not employees, but who hold an approved Entry Permit as an authorised representative of a registered employee organisation (ARREO) must be permitted to enter the premises. Before any such persons are permitted to enter the premises, the responsible person must ensure that they are in possession of a valid Entry Permit.
The Entry Permit must include at least the following:
- the name of the authorised representative;
- the name of the registered employee organisation, or the relevant branch of the organisation, of which the authorised representative is a permanent employee or officer;
- the address of the registered employee organisation or relevant branch of the organisation;
- a passport sized photograph (no more than 6 months old) of the authorised representative;
- the date of issue of the entry permit; and
- a unique number that identifies the entry permit.
Managers must also be advised that Entry Permits are valid for three years.
Managers must be advised that in such cases, these persons have the legal right to enter the premises if they suspect an occupational health and safety contravention which relates to or affects work that is being carried out by persons:
who are eligible to be members of the registered employee organisation; or
whose employment is not subject to a certified agreement by which any registered worker organisation is bound.
Any improvement notices issued by inspectors must be the subject of a Corrective Action note and dealt with within the required time limit. Where required by legislation, the authority must be notified once compliance with the notice has been achieved.
Where required, workplaces must be registered with the relevant authority, as required in each jurisdiction.
Step 4. Obtain relevant licences
Arrangements must be in place to ensure that all the required licences are obtained, are kept up-to-date and are complied with. This must include licences from the EPA for dangerous goods, radioactive substances and any other applicable licence. Where applicable long-term licences for 5 or 10 years must be sought.
Activities scheduled by legislation must be notified to the appropriate authority (e.g. WorkCover Authority, EPA, Department of the Environment, etc) within the specified time.
- Such activities may include:
- Storage of Dangerous Goods
- Storage of hazardous Wastes
- Any other activity as specified by the relevant legislation.
Civil Penalties
Managers must be advised that in some jurisdictions, the EPA is entitled to impose civil penalties for less serious environmental offences, either directly or by application to the Environment, Resources and Development Court.
Step 5. Constantly evaluate compliance
Procedure(s) must be established, implemented and maintained for periodic evaluation of the extent of compliance with legal requirements and other requirements applicable to your organisation. Full records must be kept of the outcomes of such evaluations.
General advice warning
The information on this site is of a general nature only. It does not take your specific needs or circumstances into consideration. You should look at your own situation and requirements before making any decisions. Please contact our Occupational Health and Safety Consultants for further information.
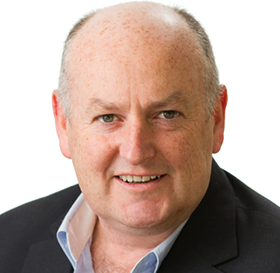